There is 78% nitrogen gas in the atmospheric air environment, as well-known. The nitrogen gas is one of the most important industrial gas types used in various purities in many industrial applications such as medical, pharmaceutical, metal, chemical industry, plastic, electronics, etc. On-site production of nitrogen gas based on the demands of customers is possible with nitrogen generators.
There are three main methods to separate nitrogen from other gas molecules in the air (oxygen, water vapour, etc.), contaminating particles or oil molecules. These are pressure swing adsorption (PSA), membrane and cryogenic processes. Cryogenically produced nitrogen is stored in cryogenic tanks. After storage, it is transported by tankers or pressurised tubes. The risk of loss during this process is high and costs are high.
Membrane-type nitrogen generators use semipermeable fibres to separate nitrogen and oxygen. In the system, the unique separation properties of different gases are utilised. While the diffusion rate of nitrogen on membrane surfaces is slow, that of oxygen and water vapour is fast. While oxygen and other gases in the compressed air diffuse out through the holes in the membrane wall and are discharged to the atmosphere, the nitrogen gas remaining in the fibres is introduced into the system. Nitrogen purity in these systems varies between 95% and 99.5%. The produced nitrogen flow rate and purity can be provided by increasing the number of modules.
Mikropor, MNG-PRO Series Nitrogen Generators with pressure swing adsorption (PSA) working principle meet industrial nitrogen gas needs by providing on-site production of high purity nitrogen gas with maximised efficiency and minimised costs.
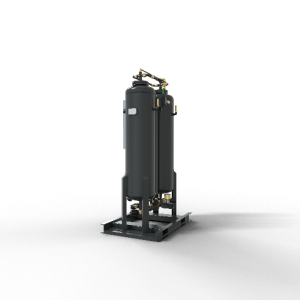
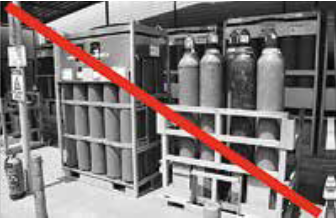
The PSA-type nitrogen generator is a two-tank adsorption system that provides on-site nitrogen production at high purities and eliminates the use of manifolds. The two tanks are connected by valve systems and compressed air lines. The tanks are filled with a granular chemical called Carbon Molecular Sieve (CMS). CMS purifies nitrogen by adsorbing oxygen and water molecules (by keeping them on its surface) thanks to the micropores in it and increases it to the desired purity levels (95-99.999%). While the pure nitrogen gas is discharged from the top line of the tank, <1% nitrogen gas is used to regenerate the other tank. This regeneration of nitrogen gas, which is used by reducing the pressure, takes up the oxygen and water adsorbed and accumulates in the other tank. Thus, the CMS granules are made reusable for the next process. A special silencer designed by Mikropor is used to reduce the noise generated during pressure relief between the tanks.
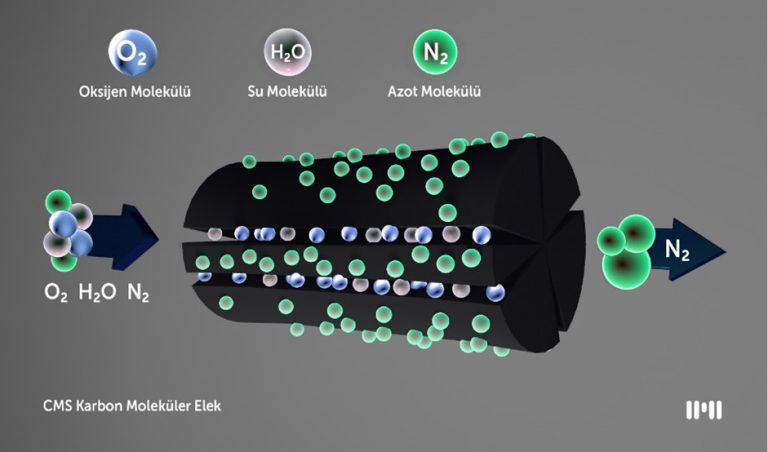
Compressed air leaving the compressor may contain oil, moisture and particles. These factors, which reduce the quality of the compressed air, must be removed before the air enters the nitrogen generator. This is because oil content reduces CMS lifetime, moisture content reduces CMS adsorption capacity, and particles penetrate CMS pores and prevent the adsorption process. For this reason, compressed air should be passed through particles, water, oil filters and air dryers before the nitrogen generator.
MNG-PRO Series, heater etc. does not contain components. In this way, electricity requirements are very low (<0.1kW). These systems can be operated continuously with regular maintenance, filtering of oil, water and particles and replacement of the CMS at the end of its life. The CMS granules have a lifetime of up to 10 years as they are continuously regenerated while the nitrogen generators are running. At the end of this period, the tanks have to be filled with new CMS granules.
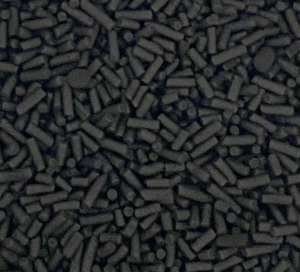
Mikropor PSA Nitrogen Generators are designed to provide ease of use. These systems provide fully automated operation and produce nitrogen gas on-site 24/7. Thanks to very low Air/Nitrogen (A/N) ratios (purity between 95% and 99.999%, ranging from a minimum of 1.2 to a maximum of 6.8), high quantities of nitrogen gas are obtained with low air consumption. This means high-efficiency gas extraction with low energy consumption. In order to control the whole system, it has a Mini PLC or HMI Color Touch Screen PLC. Thanks to this system, instant parameter values can be seen and alarms can be set for necessary situations.
Mikropor nitrogen generators produce nitrogen gas with the desired purity (95-99.999%) according to the need and up to very high flow rates (2030 cfm). The pure nitrogen gas obtained is stored in the nitrogen tank and is offered for use at the desired purity, pressure and flow rates. When the purity falls below the rate specified by the customer due to variations in inlet air quality, the system automatically switches itself off and switches to safe mode. For the more efficient and longer operation of CMS granules, Mikropor’s patented product Carbolescer (air-oil separator) and particle filter, which ensures that the nitrogen gas at the outlet is presented to the customer separated from the particles, can also be integrated into the system. The purity, flow rate and pressure of the nitrogen gas produced can be monitored instantly on the screen.
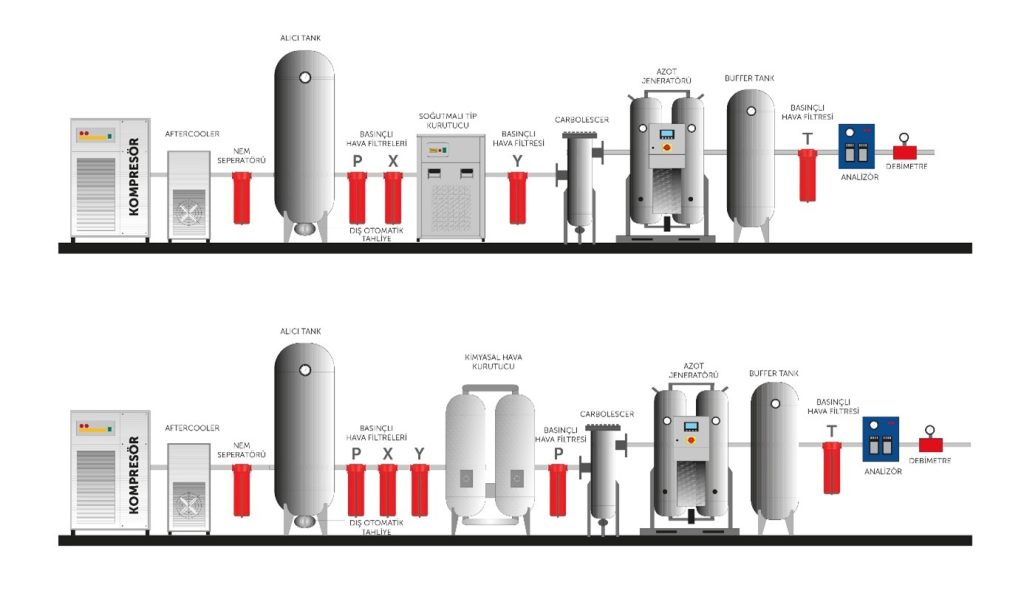
With more than 35 years of experience, Mikropor offers the Mikropor Nitrogen Purifier Deoxo System (MDX), which can be integrated into PSA Nitrogen Generators, to customers who need 99.999% purity nitrogen provided by PSA Nitrogen Generators. With this compact system, nitrogen gas can be purified up to the highest (99.999%) purity rate at dew point <38°F. When the MDX Series nitrogen purifier is integrated into the MNG-PRO Series Nitrogen Generator, the MNG-PRO Nitrogen generator is selected with low purity and the air/nitrogen ratio is reduced. With MDX connected to the nitrogen output, purity can be increased to 99.999%. In this way, nitrogen with the same capacity can be obtained with much lower air consumption. The total investment cost and energy consumption of the system consisting of MNG-PRO and MDX Series are very low.
For industrial applications requiring 99.999% pure nitrogen at a very low (-40°F) dew point, a gas dryer should be used after the Nitrogen Generator or Nitrogen Purifier System. The Mikropor Gas Dryer System (MGD) reduces the dew point down to -40°F without loss of pure nitrogen gas during the regeneration process.
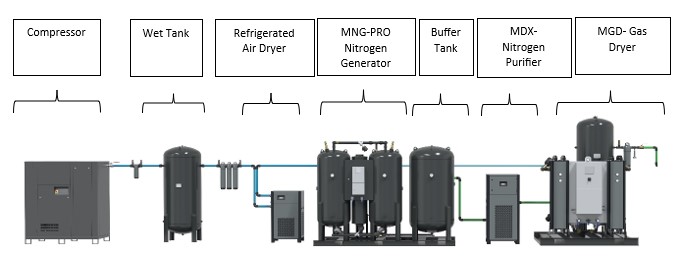
Nitrogen production in compressed air systems, in addition to the requirements of the standards, can be of various purities and various dew point levels according to the areas of use. The important thing is to determine the requirement correctly and to optimise the capacity and nitrogen quality. Therefore, extra air consumption and investment costs are avoided.
AUTHORS
Tuğba MEMILI
MİKROPOR MAK. SAN.TİC.A.Ş. / R&D Manager
tugba.memili@mikropor.com
Berkay COSKUN
MİKROPOR MAK. SAN.TİC.A.Ş. / R&D Assistant Specialist
Berkay.Coskun@mikropor.com